Shipping containers are essential for global trade, helping to move goods quickly and efficiently over long distances. Learning about the shipping container manufacturing process shows us the detailed steps needed to build these strong structures. From putting together different parts to ensuring quality control, each stage is important for making reliable containers that can handle tough conditions.
Container Assembly: Step-by-Step Process
The assembly of shipping containers involves several key steps:
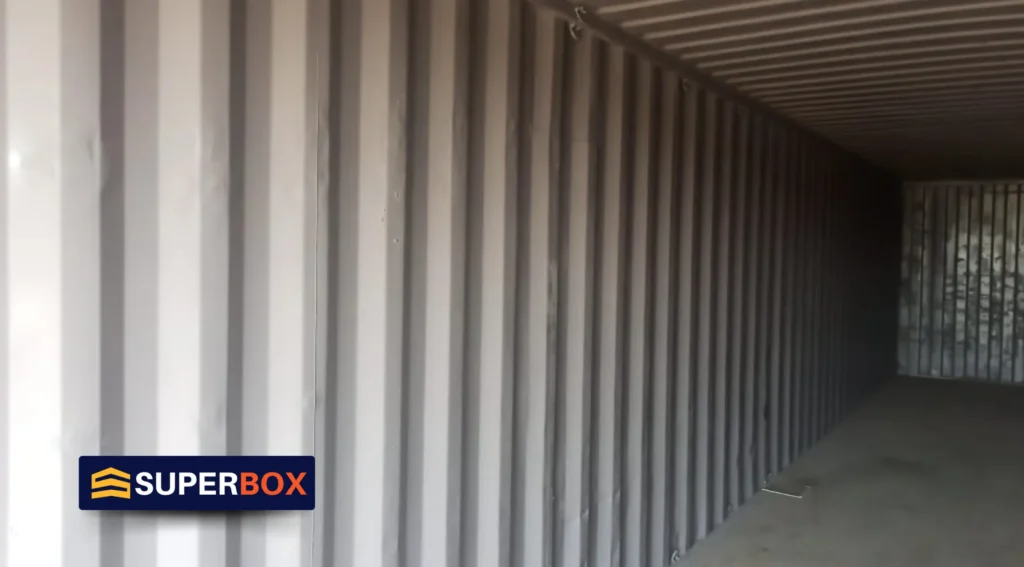
Step 1: Wall Panels
The process of building a shipping container starts with the wall panels. Large corten steel sheets are cut and shaped into these panels. To make them stronger, manufacturers often use corrugated steel, which has a wavy pattern. This design helps the containers resist bending and deformation while they are being transported. The side walls made from these panels are essential for the container’s overall strength and durability.
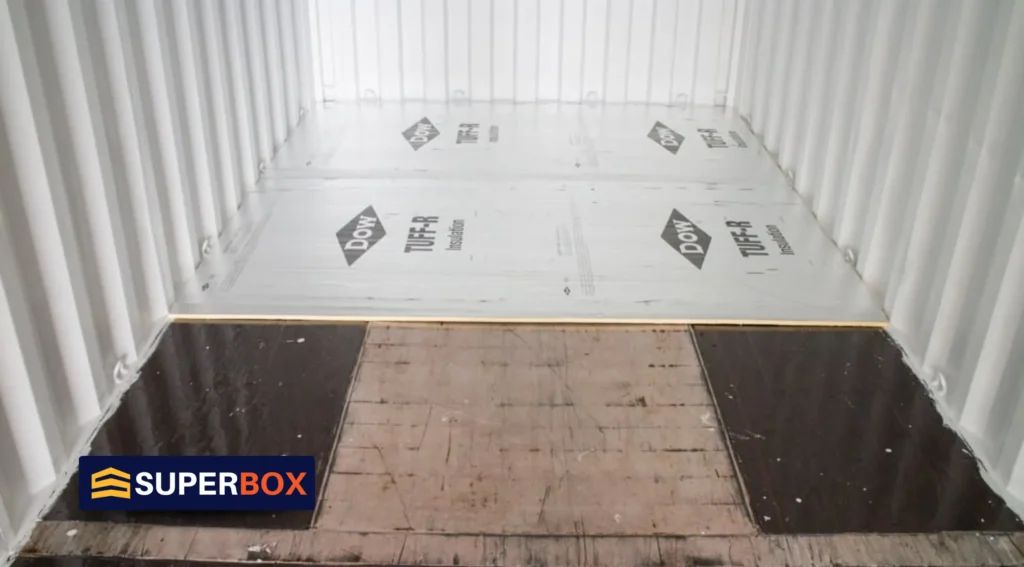
Step 2: Floor Framing
Once the wall panels are ready, the next step is to build the floor frame. This frame is made using square steel tubing, which provides a solid foundation for the container. The frame is carefully welded and screwed into place, ensuring it is stable and sturdy. A well-constructed floor frame is crucial for the container’s stability, as it supports everything inside and helps it endure various stresses during shipping.
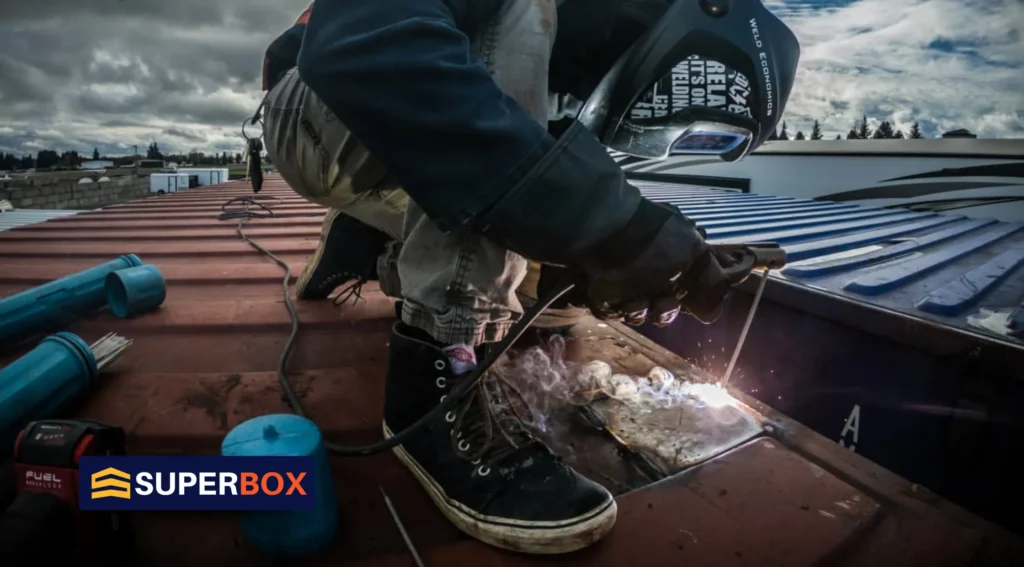
Step 3: Installing the Roof and Floor
After the floor frame is completed, the next step is to install the roof panels and secure the steel floor. These roof panels are attached to the top of the container to protect it from the elements. To keep the contents safe from rain or moisture, rubber seals are added around the edges. This step ensures that the container remains waterproof, helping to protect the items stored inside.
Step 4: Adding Door Mechanisms
The final step in assembling the shipping container is to install the door mechanisms. This includes fitting door handles and locks to the doors. These mechanisms are essential for security, allowing easy access for loading and unloading while ensuring that the contents remain safe from theft and damage. With strong locks in place, users can confidently store valuable goods in their containers.
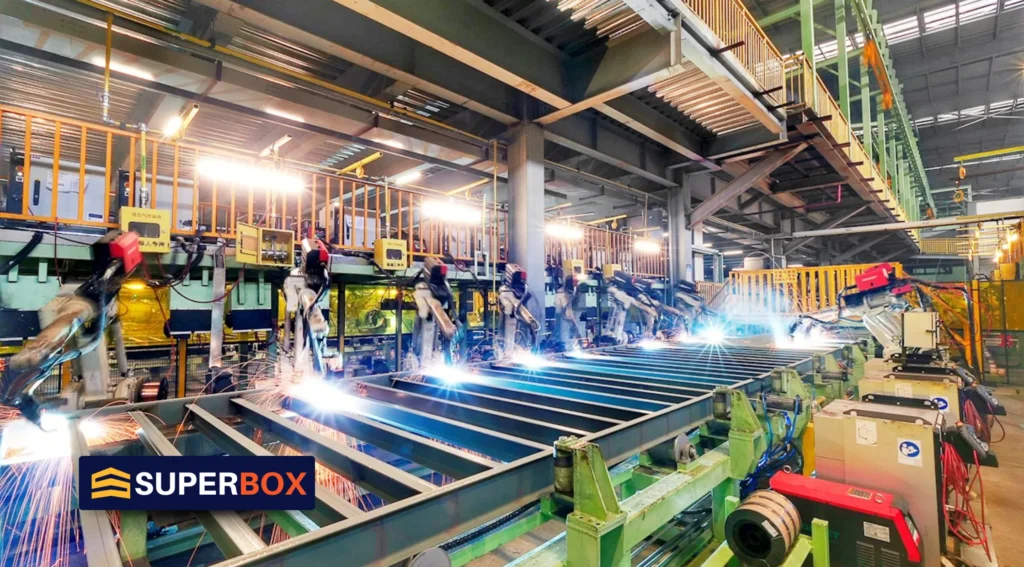
Welding Techniques in Shipping Container Manufacturing
Welding is essential in shipping container construction, securing components for strength and durability. Let’s look at the key welding methods and their importance.
- Different Welding Methods
Welding plays a crucial role in assembling shipping containers, using various techniques like MIG and TIG welding. These methods are essential for creating strong joints that hold the structure together. For example, the floor frame is welded to ensure it can support heavy loads, while the corner posts and steel panels are also secured through welding. This strong connection helps the container endure the challenges of transport and storage.
- Quality of Welds
The quality of the welds is vital for the container’s durability. Skilled welders focus on making sure that every joint is tight and secure, which contributes significantly to the overall strength of the shipping container. In addition to welding, some parts of the frame, like the floor frame, maybe both welded and screwed to enhance stability. By ensuring high-quality welds, manufacturers create containers that can reliably transport goods over long distances.
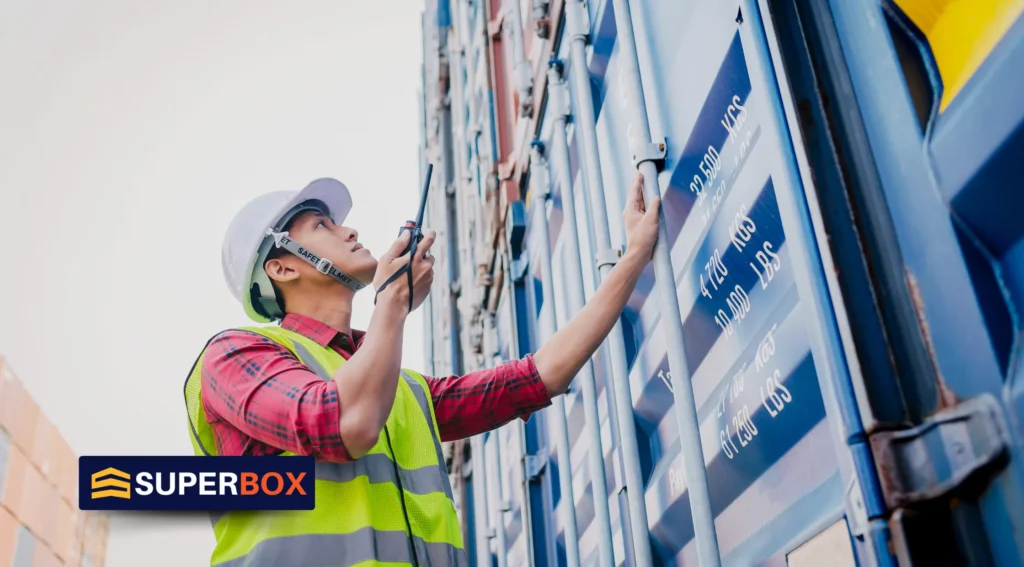
Quality Control Measures
Quality control is essential in manufacturing shipping containers, ensuring that each one is reliable and built to last. Inspections and tests help maintain high standards throughout the process.
- Inspection Procedures
Quality control is crucial in the manufacturing process, with inspections taking place at every step. Inspectors look for any flaws in the welds, panels, and overall construction to make sure only the best containers leave the factory.
- Testing Durability
Containers go through several tests to check their strength and durability. This testing ensures that each container meets industry standards and can handle tough conditions.
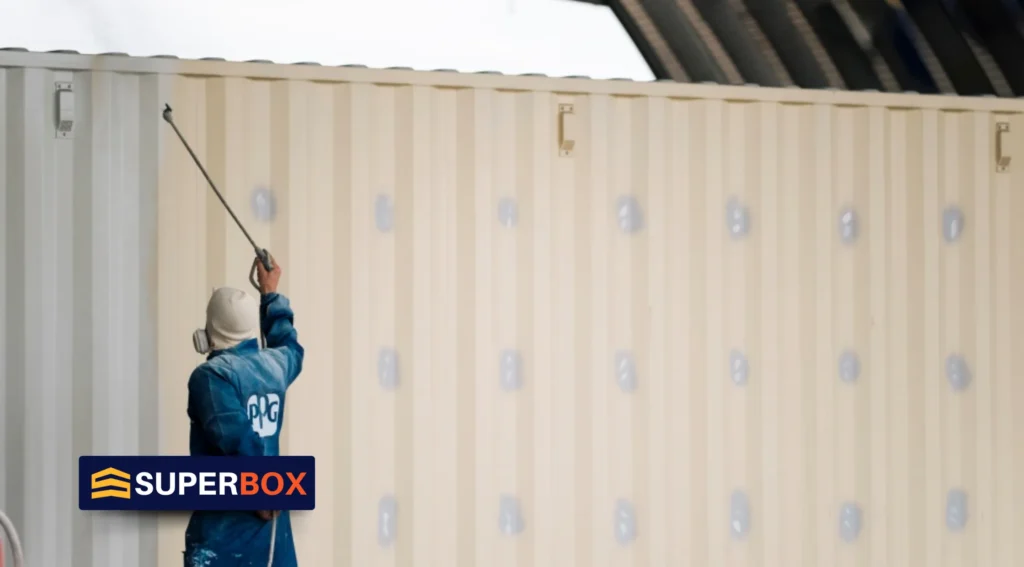
Painting and Final Touches
After the assembly process, containers are primed and painted to shield them from harsh weather conditions. This priming helps the paint adhere better and creates a protective barrier against rust and corrosion. Additional layers of protection enhance the container’s durability, ensuring it can withstand the elements for years to come. This final step is crucial in extending the lifespan of the container and maintaining its structural integrity.
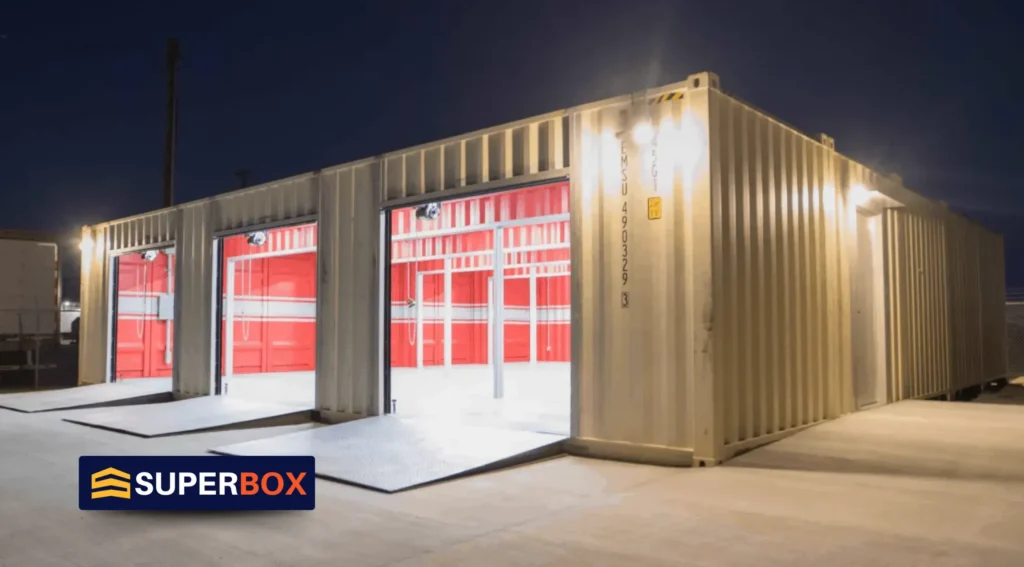
Customization and Modification
Shipping containers offer incredible versatility, allowing them to be adapted for a variety of uses. From stylish homes to functional offices, customization transforms these containers to meet specific needs.
- Adapting Containers for Specific Uses
Shipping containers can be tailored for many different purposes, including homes, offices, and storage solutions. This adaptability makes it easy to create unique spaces that fit specific needs.
- Features Added During Customization
When customizing a shipping container, various enhancements can be made. For example, marine-grade materials can be used for interior finishes, while wooden flooring adds both style and functionality to shipping container homes. Additionally, windows and extra insulation can be added to create cozy and comfortable living areas. This makes it possible to transform a basic container into a welcoming space.
Conclusion
In summary, assembling shipping containers involves several detailed steps, from building wall panels to ensuring the quality of welds. Quality control and customization are essential for improving the value and usefulness of these containers. As shipping containers become more popular for various uses, understanding how they are made—including aspects like the floor frame being screwed into place—shows their significance in both global trade and innovative construction solutions.
Discover Your Perfect Shipping Container Solution with SuperBox
SuperBox provides a wide range of high-quality shipping containers to meet your needs. Your satisfaction is our main focus, and our expert team is here to help you at every stage. Don’t wait—call us today at 210-557-006 to discover the perfect container solution for you!